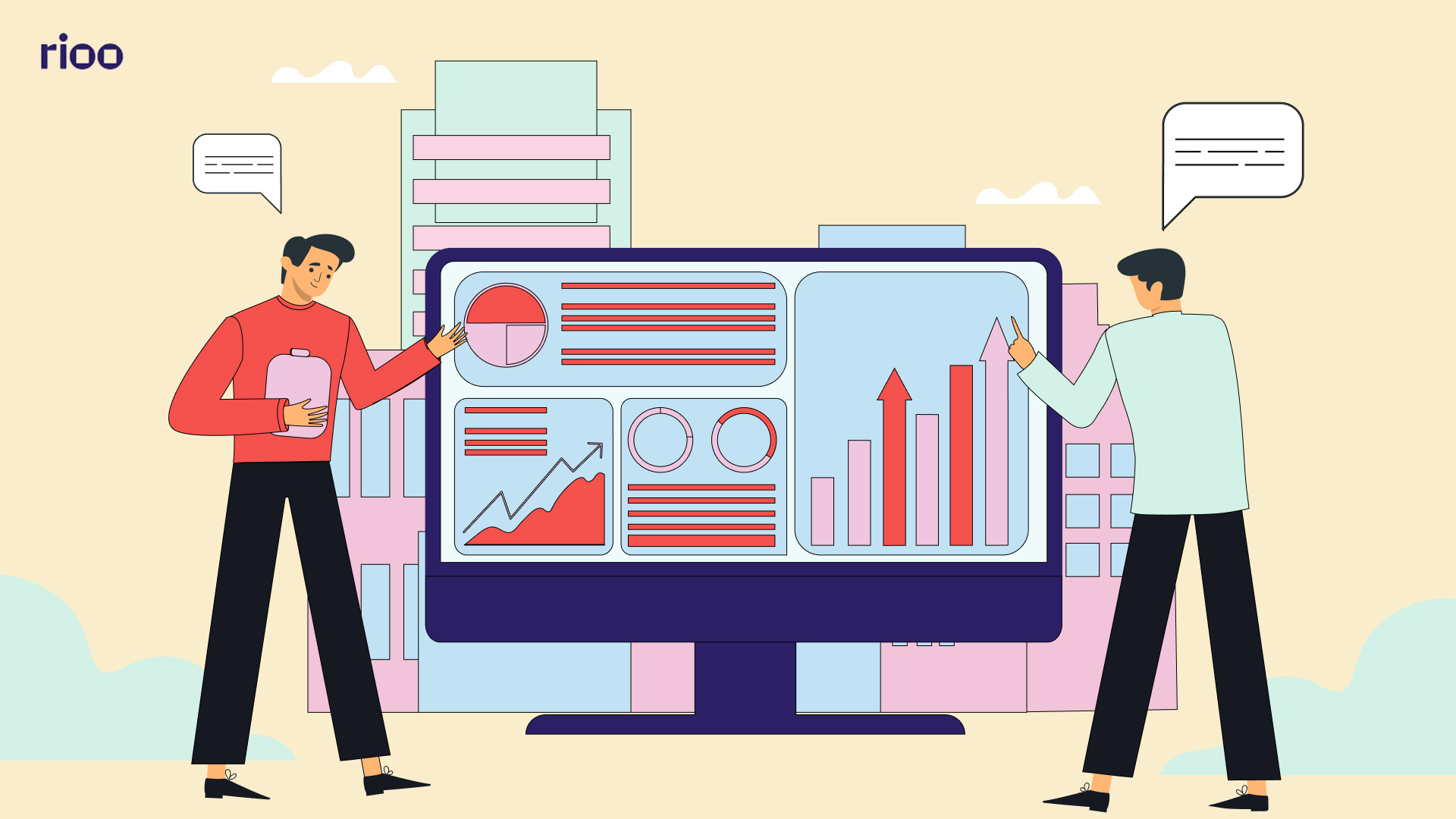
Keeping your assets running smoothly can feel like a never-ending battle. Between unexpected breakdowns and rising costs, it's easy to fall into a reactive mode.
According to a report, in 2022, the total replacement value of solid waste assets, including transfer stations and disposal facilities, was about $12 billion.
We understand that asset management can be an overwhelming task for you. But with proper asset optimization, you can extend asset lifespan through smarter maintenance.
In this guide, we'll simplify asset optimization from the ground up, starting with fundamental best practices and progressing to advanced AI-powered strategies.
TL;DR Key Summary:
Effective asset optimization can reduce downtime, extend asset lifespan, and lower operational costs. This guide covers:
-
Fundamentals: Key practices like preventive maintenance and performance monitoring.
-
Intermediate Strategies: Techniques such as digital twins, predictive maintenance, and energy optimization to reduce waste and improve efficiency.
-
Advanced AI Techniques: AI-driven tools that autonomously predict failures, optimize processes, and enhance decision-making.
-
Implementation Roadmap: A 4-step plan to audit assets, prioritize projects, pilot solutions, and scale with change management.
What is Production and Asset Management?
Production Optimization is the process of maximizing output, quality, and efficiency while minimizing costs, waste, and downtime. It involves:
-
Fine-tuning Equipment Performance: Adjusting machinery settings and maintenance schedules to ensure peak performance and reduce unplanned breakdowns.
-
Streamlining Workflows: Improving processes and eliminating bottlenecks to increase productivity and reduce delays.
-
Reducing Energy/Resource Waste: Identifying inefficiencies and optimizing energy usage and material consumption to lower costs and environmental impact.
-
Leveraging Data and Automation: Using data analysis and automated systems to make real-time adjustments, improving decision-making and operational efficiency.
Asset Management focuses on extending the life and value of physical equipment and infrastructure through:
-
Preventive/Predictive Maintenance: Identifying and addressing issues before they lead to breakdowns, reducing downtime and repair costs.
-
Cost Tracking and Budgeting: Monitoring expenses to ensure efficient use of resources and prevent overspending on maintenance and repairs.
-
Performance Monitoring: Continuously assessing asset performance to detect inefficiencies and optimize operations for longer asset life.
-
Strategic Upgrades: Implementing timely upgrades to maintain asset relevance and improve functionality.
How They Work Together:
Optimizing production requires healthy, well-managed assets. For example:
-
A factory uses predictive maintenance (asset management) to avoid machine failures, ensuring uninterrupted production (optimization).
-
Energy optimization cuts costs while reducing wear and tear on assets.
Also read: What Property Owners Expect From Leasing Managers During Transitions
The Fundamentals of Production Optimization
If you want to improve efficiency and extend the life of your assets, you need to start with the basics.
Key Metrics to Track
-
OEE (Overall Equipment Effectiveness)
-
OEE measures how well your equipment is actually performing compared to its full potential.
-
Formula: Availability × Performance × Quality
-
Example: If a machine runs at 90% availability, 85% speed efficiency, and 95% quality rate, its OEE is 72.7% (0.90 × 0.85 × 0.95).
-
Goal: World-class OEE is 85%+, if yours is below 60%, there’s major room for improvement.
-
-
Cycle Time Variance
-
Tracks how much production times fluctuate.
-
Why it matters: Inconsistent cycles lead to bottlenecks and wasted capacity.
-
Fix: Standardize processes and train operators to reduce deviations.
-
-
Yield Rates
-
Measures how much usable product you get vs. waste/scrap.
-
Example: If you input 1,000 units but only 920 meet quality standards, your yield is 92%.
-
Improvement Tip: Small tweaks (like calibrating machines more often) can boost yield by 5–10%.
-
Essential Tools for Asset Optimization
These proven tools help organizations transition from reactive fixes to proactive optimization:
Preventive Maintenance (PM) Schedules
-
Calendar-based Servicing: Regularly scheduled servicing based on a fixed calendar, ensuring timely maintenance intervals.
-
Manufacturer-recommended Tasks: Maintenance activities suggested by the equipment's manufacturer to maintain optimal performance.
-
Routine Lubrication: Regular application of lubricants to reduce wear and tear on moving parts.
-
Calibration: Ensuring equipment is correctly calibrated to maintain accurate operation and prevent errors.
-
Inspections: Scheduled checks to identify potential issues before they escalate into costly repairs.
-
Condition Monitoring Checkpoints: Monitoring equipment performance through sensors or diagnostics to detect abnormal conditions.
-
Parts Replacement Timelines: Replacement of parts based on predetermined lifespans or performance criteria to prevent failure.
Lean Manufacturing (5S, Kaizen)
-
-
5S: Organizes and maintains a clean workspace to improve efficiency, reduce downtime, and prolong equipment life by preventing wear and tear.
-
Kaizen: Encourages continuous improvement, fostering small, incremental changes that optimize asset performance and reduce waste over time.
-
Value Stream Mapping: Identifies inefficiencies in asset usage, helping streamline workflows and enhance asset utilization.
-
Visual Management: Uses visual tools to track asset performance and identify issues quickly, minimizing downtime and ensuring efficient asset management.
-
Standardized Work: Establishes consistent processes for asset maintenance and operations, ensuring optimal performance and reducing errors or variances in asset usage.
-
Why These Basics Matter
These foundational tools, while basic, deliver productivity gains within months of implementation, providing a solid base before advancing to more complex solutions.
Want to automate these metrics without complex software? RIOO's workflows and customizations can provide the right solution for you. [Book a Demo now].
Intermediate Optimization Strategies for Smarter Asset Management
Once you’ve mastered the basics, it’s time to level up with industry-proven intermediate strategies.
These solutions bridge the gap between simple fixes and advanced AI, delivering measurable results without overwhelming your team. Let’s break down the top three:
1. Digital Twin Technology: Test Before You Invest
Digital twin technology is a game-changing tool in asset optimization. Digital twin technology creates a real-time virtual replica of physical assets by integrating sensor data through advanced modeling software.
This builds and updates detailed 3D representations to simulate and analyze operations dynamically.
How Digital Twins Work
-
Data Collection: Sensors (IoT) on physical assets feed real-time data (temperature, vibration, output, etc.) into the digital twin.
-
Virtual Modeling: Advanced software uses this data to build and update a 3D digital model.
-
Simulation & Analysis: Run "what-if" scenarios (e.g., equipment upgrades, process changes) without disrupting actual operations.
-
Actionable Insights: Identify inefficiencies, predict failures, or test optimizations before implementing them in the real world.
How it optimizes assets:
-
Risk-free experimentation: Test layout changes, new equipment, or process tweaks in a digital environment.
-
Predict bottlenecks: Identify underperforming assets before they slow down production.
-
Reduce waste: Optimize material flow and energy usage virtually.
Pro Tip: Start with a single critical asset (like a high-value machine) before scaling to full production lines.
2. Predictive Maintenance: Stop Failures Before They Stop You
Reactive maintenance is the "fix it when it breaks" approach, which results in costly unplanned downtime, emergency repairs, and lost productivity.
On the other hand, Predictive maintenance (PdM) uses IoT sensors to monitor equipment conditions in real-time. Machine learning forecasts failures, allowing for scheduled repairs during planned downtime and preventing costly unplanned breakdowns.
Asset Optimization Benefits:
-
20% or longer asset lifespan
-
Near-zero unplanned downtime
3. Energy Optimization: Cut Costs Without Cutting Output
Energy, which accounts for 15–30% of operational costs, can be reduced through smart energy optimization strategies while maintaining productivity.
Key Tactics:
-
Smart load balancing: Shift energy-intensive tasks to off-peak hours.
-
AI-driven HVAC optimization: Adjust temps based on occupancy/weather.
-
Sub-metering: Track energy use per machine to find inefficiencies.
These intermediate strategies share one goal: maximizing asset value while minimizing waste. Up next, we will also provide an implementation roadmap for the strategic deployment of these techniques.
RIOO’s property management platform bundles these tools into one system, so you can implement fast without IT headaches. [Get in touch now].
Implementation Roadmap for Asset Optimization Success
Asset optimization isn't about making random upgrades. It's a strategic process that maximizes equipment performance while minimizing costs.
Whether you're managing a single facility or a global portfolio, this 4-step roadmap (backed by real-world deployments) will help you implement changes that deliver measurable results.
Step 1: Audit Current Assets
Know What You’re Working With. Before optimizing, you need a clear snapshot of your assets.
How to do it right:
-
Inventory all equipment: List critical machines, age, condition, and maintenance history.
-
Track performance metrics: Collect data on uptime, energy use, and failure rates.
-
Identify pain points: Flag assets causing frequent downtime or inefficiencies.
Step 2: Prioritize Projects by Potential ROI
Focus on High-Impact Upgrades. Not all optimizations are equal. Use this sample matrix to rank projects:
Key questions:
-
Which upgrades align with business goals (cost-cutting vs. output growth)?
-
What’s the payback period? (Aim for <12 months for quick wins.)
Step 3: Pilot Small
Test Before Full Commitment. Begin with a controlled pilot (e.g., a single production line or facility).
Best practices:
-
Set clear KPIs (e.g., Reduce unplanned downtime by 10% in 3 months).
-
Involve frontline teams, they spot real-world hicapps.
-
Document lessons learned before scaling.
Step 4: Scale with Change Management
Optimization fails when teams resist change.
Proven tactics:
-
Train early adopters to champion new tools.
-
Phase rollouts (e.g., by department vs. all at once).
-
Celebrate wins (show “Before/After” cost savings).
3 Red Flags to Avoid
-
Skipping the audit: Optimizing the wrong assets wastes budget.
-
Over-automating: Not every process needs AI (start with high-impact areas).
-
Ignoring culture: Even the best tech fails if operators don't trust it.
Advanced AI-Driven Optimization: The Future of Asset Management
AI and machine learning enable systems to learn from data, identify complex patterns, and predict outcomes by iteratively improving performance without explicit programming.
These technologies improve by analyzing large datasets, refining predictive models for accurate classification and forecasting.
AI enhances asset optimization by turning raw data into actionable insights through data collection, analysis, and autonomous decision-making.
-
Data Collection & Analysis
-
Sensors and IoT devices gather real-time performance data (vibration, temperature, energy use).
-
Machine learning models detect patterns, like early signs of equipment wear.
-
-
Autonomous Decision-Making
-
Self-adjusting systems (e.g., smart grids that automatically rebalance energy loads).
-
Prescriptive AI acts without human input: "Shift production to Line B while repairing Line A."
-
Where traditional methods reach their limits, AI-powered optimization unlocks the next frontier of efficiency. These cutting-edge technologies don't just report problems, they anticipate and solve them autonomously:
Autonomous Optimization
Self-correcting production systems use reinforcement learning algorithms to improve operational efficiency autonomously:
-
Rebalance production schedules autonomously
-
Optimize energy consumption dynamically
Prescriptive Analytics
AI that doesn't just predict, but prescribes, analyzing millions of data points to recommend actions like:
-
"Reroute Batch #2071 to Line B to prevent a three-hour downtime."
-
"Replace bearing in Compressor C12 during next PM cycle"
-
"Increase lubricant viscosity by 15% for summer operations"
Blockchain for Asset Tracking
Blockchain is a decentralized ledger technology that records transactions across multiple computers securely, making data tamper-proof and transparent to all participants.
It uses a distributed network to create secure, unchangeable records of asset histories and maintenance, which prevents tampering and enhances trust and compliance.
Here are the top 5 common fundamentals related to blockchain technology:
-
Decentralization: By distributing the data across multiple nodes, blockchain eliminates the need for a central authority. This ensures transparency and reduces the risk of data manipulation or single points of failure in asset tracking.
-
Immutability: Once asset data is recorded on the blockchain, it cannot be changed. This ensures that the asset's history, including ownership, maintenance records, and conditions, remains secure and unaltered, building trust in the asset.
-
Consensus Mechanisms: These protocols ensure that all parties agree on the validity of asset-related transactions. This enhances the accuracy of asset tracking and prevents fraudulent claims or discrepancies in asset records.
-
Cryptography: Cryptographic techniques safeguard sensitive asset data. This ensures that only authorized parties can access or modify the information, maintaining security and privacy throughout the asset lifecycle.
-
Smart Contracts: By automating asset-related processes such as transfers or maintenance tasks, smart contracts ensure that predefined conditions are met without human intervention. This improves operational efficiency, accuracy, and reduces the risk of errors in asset management.
Blockchain's growing importance in secure data management arises from its capacity to ensure trust, transparency, and data immutability. This is critical for applications demanding reliable data integrity.
As industries seek to enhance data security and traceability, blockchain is becoming essential, particularly in asset tracking, where it helps ensure the authenticity and provenance of assets in real-time.
While revolutionary, these technologies require careful implementation. The next section reveals the step-by-step framework successful plants follow to avoid costly missteps.
Up next, let's discuss how you can get started with RIOO to ease the optimization process.
Suggested read: The Psychology of Tenant Satisfaction: What Keeps People from Moving Out
How RIOO Transforms Asset Optimization Beyond Traditional Solutions?
Traditional asset management depends heavily on reactive fixes and manual tracking, which can trap teams in inefficient cycles.
RIOO offers a smarter, proactive approach to asset optimization, featuring automated tracking and early issue detection. Here's what sets RIOO apart:
From Manual Tracking to Automated Intelligence
-
Smart digital registers automatically track asset health and maintenance history.
-
Live dashboards highlight potential issues before they become problems
-
Real-world impact: Clients transition from cumbersome manual audits to instant visibility
From Reactive Fixes to Preventative Care
-
Early warning systems detect developing equipment issues
-
Maintenance schedules that adapt to actual usage patterns
-
Tangible results: Significant reductions in unplanned downtime across client facilities
Curious how AI optimization could work in your facility? RIOO's assistance identifies high-impact starting points. [Get Insights]
Final Thoughts: Key Takeaways & Next Steps
Effective asset optimization requires moving beyond traditional reactive approaches. As we've explored:
-
Visibility comes first: Accurate asset audits form the foundation for improvement
-
Data beats guesses: Prioritize projects based on evidence, not intuition
-
Small tests lead to big results: Structured pilots create momentum for scaling
-
Prevention pays: Early intervention maintains equipment reliability
RIOO enables property managers with the tools they need to optimize assets proactively. From real-time maintenance tracking and predictive alerts to comprehensive financial reporting, RIOO streamlines your operations and enhances asset management.
Discover RIOO's Solutions and build your specific optimization goals.
Don’t miss out, get your RIOO
Subscribe to our newsletter and receive updates on the go