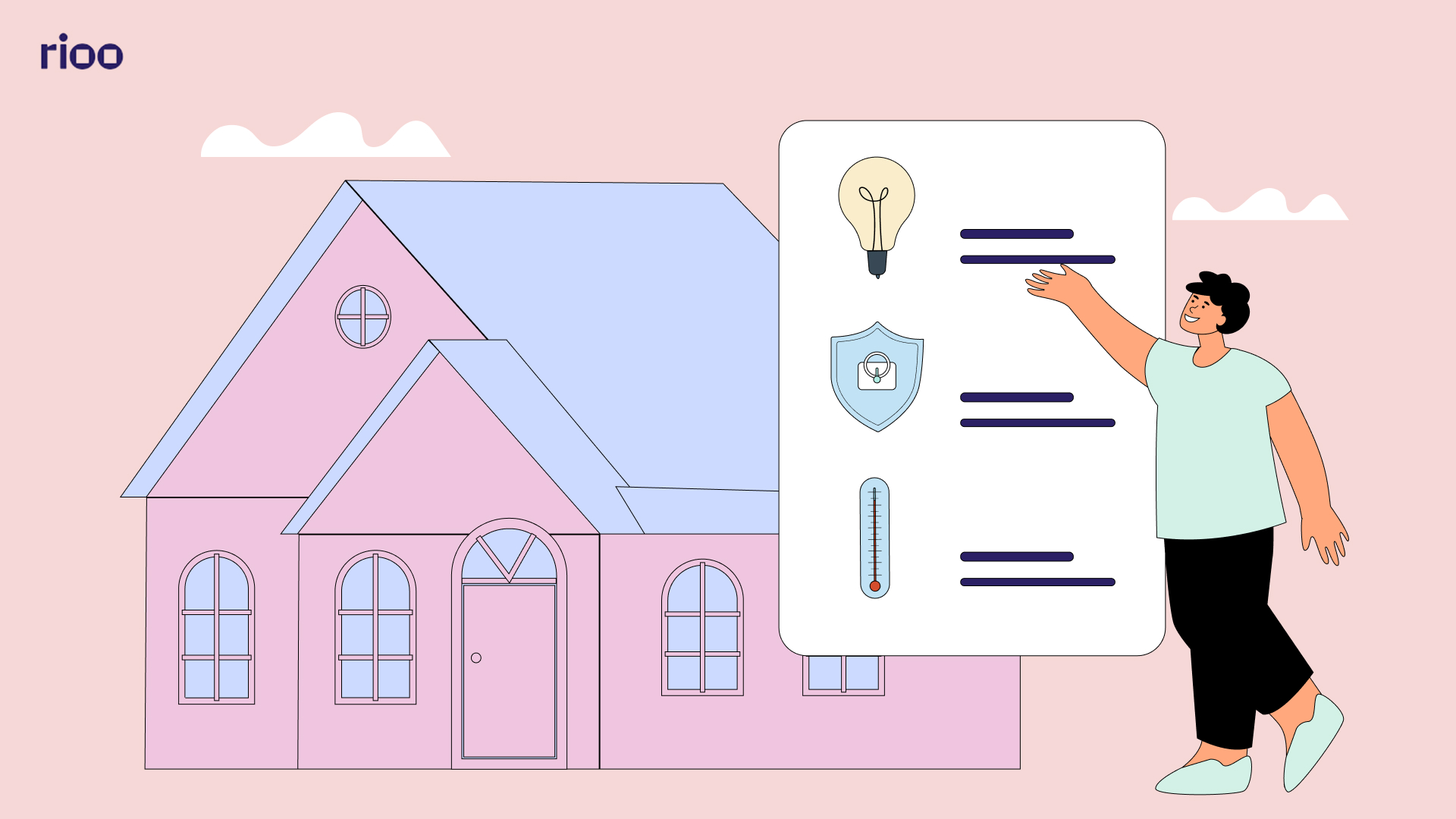
Facility managers face enough daily challenges without the added stress of unexpected breakdowns. Missing early warning signs can mean costly emergency repairs and unnecessary headaches.
That's why properly assessing your facility's condition and systematically checking HVAC, electrical, and structural systems is critical.
This guide will show you how to efficiently evaluate your facility's health, helping you catch problems early, reduce costly downtime, and maintain smooth operations. With the right approach, you can stop guessing about equipment conditions and start making informed maintenance decisions.
Understanding Condition Assessment in Facility Management
At its core, assessing condition is like giving your facility a regular health check-up. It systematically evaluates the physical state and operational performance of all your building assets.
Unlike reactive maintenance (waiting for something to break), condition assessment is a proactive approach. It helps you:
-
Spot early warning signs (like unusual vibrations or small leaks)
-
Measure performance decline (reduced efficiency in equipment)
-
Document wear patterns (corrosion, cracks, or material fatigue)
Why This Matters for Your Facility
-
Cost Control
-
Finding a failing bearing early instead of missing it till it becomes a heavy expense.
-
-
Safety Assurance
-
Regular electrical inspections prevent fire hazards
-
Structural assessments avoid catastrophic failures
-
-
Budget Planning
-
Accurate condition data helps you:
-
Prioritize which assets need immediate attention
-
Plan multi-year replacement budgets
-
Justify capital expenditures to stakeholders
-
-
Want to upgrade from clipboards to smart condition monitoring? See how RIOO's automated assessments work [Live Demo]
Also Read: Why a Portal-First Approach is Changing the Way Tenants Interact with Property Managers
Step-by-Step Process for Effective Condition Assessments
Step 1: Inventory All Assets - Your Foundation for Smart Facility Management
Imagine trying to fix a problem when you don't even know what equipment you have. That's why creating a complete asset inventory is the first step in assessing condition meaning.
It gives you the full picture of what needs to be monitored and maintained. Without this foundation, you're essentially blindfolded, risking unexpected breakdowns and costly emergency repairs.
How to Build Your Asset Inventory Right:
-
Identify All Critical Equipment
-
Start with systems that would cause major operational disruptions if they failed
-
Common high-priority assets include:
-
HVAC systems (chillers, boilers, air handlers)
-
Electrical systems (transformers, switchgear)
-
Plumbing (water heaters, pumps)
-
Structural elements (roofing, elevators)
-
Safety systems (fire alarms, sprinklers)
-
-
-
Implement Smart Tracking Methods
-
Physical Tags: Use durable barcode labels or QR codes that withstand environmental conditions
-
Digital Tracking: Create a centralized database where each asset has:
-
Unique ID number
-
Location details (building, floor, room)
-
Manufacturer specifications
-
Warranty information
-
-
-
Choose the Right Tools
-
Pen-and-paper checklists (for small facilities just starting out)
-
Spreadsheets (better organization but limited functionality)
-
Dedicated software like RIOO's asset registry that offers:
-
Automated maintenance reminders
-
Lifecycle tracking from installation to replacement
-
-
Pro Tips for Success:
-
Prioritize by impact: Focus first on assets where failure would be most costly or dangerous
-
Include hidden assets: Don't forget about equipment behind walls or in mechanical rooms
-
Make it a team effort: Involve maintenance staff who know the equipment best
-
Schedule regular updates: Review and update your inventory at least annually
RIOO's asset management system gives you complete visibility and control over your facility's critical systems. [See how it works]
Now that you've built your complete inventory, we'll show you how to determine exactly what to look for when assessing each asset's condition, moving from simply knowing what you've to understanding how well it functions.
Step 2: Define Assessment Criteria
An asset inventory is a complete record of all critical equipment and systems in your facility. It’s the essential first step for assessing conditions; you can’t monitor what you haven’t identified.
Here are the key metrics to track when assessing facility conditions:
1. Physical Condition
Look for visible signs of wear and damage, such as:
-
Rust, corrosion, or peeling paint (indicates moisture exposure)
-
Leaks or water stains (plumbing or roof issues)
-
Cracks in walls, floors, or foundations (structural concerns)
Why it matters: Small problems (like a minor leak) can turn into costly repairs if ignored.
2. Performance Metrics
Check how well equipment and systems are functioning:
-
Energy efficiency (e.g., HVAC using more power than usual)
-
Output levels (e.g., reduced water pressure in pipes)
-
Unusual noises/vibrations (early signs of mechanical failure)
Why it matters: Declining performance often means an asset is nearing failure.
3. Compliance & Safety Standards
Ensure everything meets regulations, including:
-
Fire safety systems (alarms, extinguishers, exits)
-
Electrical wiring (no exposed or frayed wires)
-
Accessibility standards (ADA compliance for ramps, doors)
Why it matters: Non-compliance risks fines, accidents, or lawsuits.
Pro Tip: Use a standardized checklist to ensure nothing gets missed.
Need help tracking condition metrics? RIOO’s facility management software logs damage reports, performance trends, and compliance checks in one place, so you can act before small issues become big problems. [Learn More].
Step 3: Choose Assessment Methods
To properly evaluate facility conditions, you need the right approach. Start with visual inspections, walkthroughs with checklists to spot obvious issues like leaks or cracks.
For critical equipment, use predictive tools like vibration sensors or thermal imaging to catch problems before they cause failures.
For deeper insights, rely on data-driven methods that pull information from IoT devices or past maintenance logs to identify hidden trends.
Step 4: Assign Priority Levels
Not all issues require immediate attention. Use a risk matrix to rank problems based on how likely they are to fail and how severe the impact would be.
For instance, a broken HVAC system during winter would require urgent attention due to its high impact on comfort and safety, whereas a flickering light in a storage room can be addressed later, as it has minimal impact.
Step 5: Document Findings & Take Action
After assessing, record everything clearly, use digital reports with photos and notes to track issues.
Then, plan next steps: schedule urgent repairs, budget for future upgrades, and adjust maintenance plans to prevent repeat problems. Proper documentation ensures nothing gets overlooked and helps justify spending.
Why This Works:
-
Visual checks catch surface problems quickly.
-
Predictive tools prevent unexpected breakdowns.
-
Data analysis reveals long-term risks.
-
Prioritization ensures critical issues get fixed first.
-
Documentation keeps repairs organized and accountable.
Using structured methods for assessments saves time, money, and headaches. Tools like RIOO's facility management software can automate inspections, track trends, and generate work orders, making the entire process smoother. [Learn more].
Common Challenges & Solutions in Assessing Condition
Assessing conditions in facility management helps you catch problems early, but the process isn’t always smooth. Here are common hurdles and how to solve them:
Challenge #1: Inconsistent Data Collection
-
Problem: Paper checklists get lost, and notes are hard to decipher. This makes assessing conditions unreliable over time.
-
Solution: Use mobile apps with digital forms.
-
Standardize fields (e.g., dropdowns for "Good/Fair/Poor" ratings).
-
Attach photos/videos to reports for clarity.
-
Example: RIOO’s inspection tool auto-syncs data to your dashboard.
-
Challenge #2: Too Many Assets to Track
-
Problem: Assessing condition for hundreds of assets feels overwhelming. Where do you start?
-
Solution: Prioritize critical systems first:
-
Life-safety items (fire alarms, elevators).
-
High-cost systems (HVAC, roofing).
-
Non-urgent assets (landscaping, paint).
-
Pro Tip: Use ABC analysis to rank assets by risk.
-
Challenge #3: Staff Pushback on New Processes
-
Problem: Teams resist changes to how they assess conditions, fearing extra work.
-
Solution: Show the "why" with real results:
-
Share before/after cases (e.g., "We saved a certain percentage in catching a failing pump early").
-
Train with hands-on demos, not just manuals.
-
Start small (e.g., pilot one department).
-
Also Read: Reducing Downtime: Why Efficient Task Handling Matters in Facility Maintenance
How Technology Simplifies Condition Assessments
Assessing conditions manually is time-consuming and prone to human error. Modern tools automate this process, making it faster, more accurate, and proactive. Here's how technology transforms what assessing conditions means for facility managers:
Automated Alerts: Catch Problems Before They Escalate
-
How it works: Systems can monitor equipment 24/7, flagging anomalies (e.g., unusual energy spikes, temperature fluctuations).
-
Why it matters: Prevents emergency breakdowns with timely warnings.
Historical Trends: Predict Failures with Data
-
How it works: Analyzes past performance to forecast wear and tear.
-
Compare decay rates of roofing materials over 5 years.
-
Track elevator maintenance frequency to schedule preemptive repairs.
-
-
Why it matters: Extends asset lifespan with predictive care.
Integration: Streamline Repairs with CMMS
-
How it works: Sync condition data with your CMMS (Computerized Maintenance Management System) to auto-generate work orders.
-
Example: A leaking pipe alert instantly creates a prioritized task for your plumber.
-
Why it matters: Reduces repair delays with seamless workflows.
RIOO’s condition monitoring turns data into actionable insights so you can fix issues before they cost you.
Let's understand how RIOO can help you access conditions.
How RIOO Organizes Condition Assessments
Condition assessments shouldn’t rely on outdated spreadsheets or missed site visits. RIOO brings structure, visibility, and consistency to how you monitor asset health.
So, you can stay ahead of maintenance needs before they spiral into major issues. Here's what you can expect:
1. Scheduled Assessments: Plan recurring inspections and log condition scores in a centralized platform. Every check is documented. No data is lost in emails or paper forms.
2. Asset-Based Maintenance Workflows: Flag issues during inspections and auto-convert them into service requests. All tasks are linked back to the asset, ensuring full repair history and accountability.
3. Real-Time Status & Priority Views: Sort and prioritize open issues based on urgency, location, or asset type. The team knows what to fix first.
4. Centralized Reporting for Smarter Planning: Generate detailed reports on inspection trends, failure types, and frequency. Use these insights to plan budgets and optimize long-term maintenance cycles.
Conclusion
Assessing facility conditions doesn’t have to mean endless manual inspections and guesswork. By implementing systematic assessments and choosing RIOO, it's easy to catch small issues before they become costly emergencies.
RIOO’s condition monitoring platform gives you real-time alerts, predictive insights, and automated workflows, all in one place. Stop reacting to breakdowns and start preventing them.
Try RIOO today and experience better facility management.
Book your personalized RIOO demo now →
Don’t miss out, get your RIOO
Subscribe to our newsletter and receive updates on the go