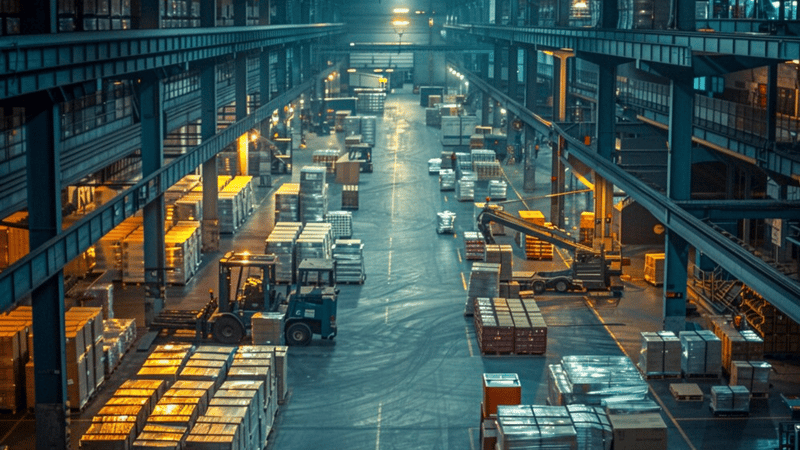
Managing a warehouse involves handling a lot of equipment, from conveyor belts to forklifts and refrigeration systems. If any of these break down unexpectedly, it can lead to costly repairs, delays, and lost revenue. This is where predictive maintenance for warehouses can make a big difference. Instead of waiting for equipment to fail, this approach helps warehouse owners prevent breakdowns before they happen, saving both time and money.
Stay Ahead of Breakdowns with Predictive Maintenance
Predictive maintenance is a smart way to keep warehouse equipment running efficiently. Instead of waiting for machines to fail, this approach relies on technology to detect early warning signs of wear and tear. Sensors installed on equipment track key factors like temperature, vibration, and energy usage. This real-time data is analyzed by software to identify potential issues before they turn into major breakdowns.
Unlike regular maintenance, which follows a set schedule regardless of need, predictive maintenance focuses on actual equipment conditions. This prevents unnecessary servicing and reduces maintenance costs. It also avoids the risks of reactive maintenance, where repairs only happen after a failure, leading to downtime and expensive emergency fixes. Predictive maintenance for warehouses ensures that repairs are done at the right time, improving efficiency, extending equipment lifespan, and preventing costly disruptions in warehouse operations.
The Role of Predictive Maintenance in Industrial Property Management
For businesses in industrial property management, maintaining warehouses efficiently is essential for long-term profitability. Predictive maintenance helps property managers and owners avoid costly breakdowns, ensuring that equipment and infrastructure remain in top condition. A well-maintained warehouse not only reduces unexpected repair expenses but also enhances the overall value of the property.
When a warehouse operates smoothly, it becomes more attractive to tenants looking for reliable and efficient storage or distribution spaces. Businesses prefer facilities where they won’t have to worry about frequent equipment failures or operational disruptions. This leads to higher occupancy rates, stable rental income, and long-term tenant satisfaction.
Additionally, predictive maintenance helps in budgeting more accurately for repairs and replacements, preventing sudden financial strain. By integrating predictive maintenance strategies, industrial property owners can reduce risks, enhance operational efficiency, and ensure their warehouses remain competitive in the market.
How Predictive Maintenance Saves Costs
Predictive maintenance for warehouses is a smart strategy that helps reduce expenses while keeping operations efficient. Here’s how it saves costs:
-
Reduces Equipment Downtime – When machines fail without warning, warehouse operations suffer delays and financial losses. Predictive maintenance detects early warning signs, allowing timely repairs and preventing unexpected breakdowns.
-
Lowers Repair Costs – Addressing minor issues early is far cheaper than replacing entire systems. With predictive maintenance, warehouse owners can schedule repairs at convenient times, avoiding costly emergency fixes.
-
Extends Equipment Life – Regular monitoring keeps machinery in top shape for longer, reducing the frequency of replacements and cutting down capital expenses.
-
Improves Energy Efficiency – Faulty equipment consumes excess energy, driving up electricity bills. Predictive maintenance ensures machines run efficiently, lowering energy costs.
-
Enhances Safety – Malfunctioning equipment poses safety hazards for workers. Using facility maintenance software to track performance helps prevent workplace accidents, reducing liability and medical costs.
From Reactive to Proactive: Steps to Smarter Warehouse Maintenance
Use Sensors and IoT Devices
Modern warehouses rely on heavy machinery, and unexpected failures can be costly. Installing IoT sensors on key equipment allows real-time tracking of temperature, vibration, and energy usage. These smart devices detect small performance issues before they turn into major failures, ensuring smooth operations and reducing downtime.
Invest in Facility Maintenance Software
Data-driven decision-making is the key to efficient maintenance. A reliable facility maintenance software gathers real-time data from sensors, analyzes performance trends, and sends alerts when repairs are needed. It also helps warehouse managers schedule inspections, track past maintenance records, and optimize resource allocation for better cost control.
Analyze Historical Data
Every warehouse has patterns in equipment performance and failure rates. Studying historical maintenance data helps identify weak points and predict which machines are at higher risk of breakdowns. With this insight, warehouse owners can proactively schedule repairs, preventing costly disruptions and unexpected operational failures.
Train Staff on Predictive Maintenance
Technology alone isn’t enough—employees need the right skills to use it effectively. Training staff to interpret sensor alerts and respond to maintenance warnings ensures quick action. When workers understand predictive maintenance tools, they can prevent minor issues from escalating, reducing downtime and improving overall efficiency.
Schedule Regular Equipment Checkups
While predictive maintenance minimizes emergency breakdowns, occasional manual inspections are still essential. Some issues require a hands-on approach to detect hidden wear and tear. Regular checkups complement technology-driven maintenance, ensuring all equipment runs smoothly and preventing unexpected failures that could disrupt warehouse operations.
RIOO: A Smart Solution for Warehouse Maintenance
Warehouse owners need a system that simplifies maintenance and property management. RIOO, a leading industrial property management solution, provides an all-in-one platform for monitoring assets, handling maintenance requests, and managing financials.
How RIOO Supports Predictive Maintenance
- Real-Time Monitoring: RIOO helps track warehouse equipment health, enabling managers to detect early warning signs.
- Automated Maintenance Scheduling: The platform ensures timely servicing based on equipment performance data.
- Financial Management: RIOO provides cost insights on repairs and maintenance, helping owners optimize budgets.
- Customizable Portals: Warehouse managers can streamline operations with tailored maintenance dashboards.
Final Thoughts
Predictive maintenance for warehouses is a game-changer, helping owners reduce expenses, prevent downtime, and improve equipment efficiency. By leveraging advanced tools like RIOO, warehouses can automate maintenance processes, optimize financial management, and ensure long-term cost savings. Investing in predictive maintenance today leads to a more profitable and efficient warehouse operation in the future.
Don’t miss out, get your RIOO
Subscribe to our newsletter and receive updates on the go